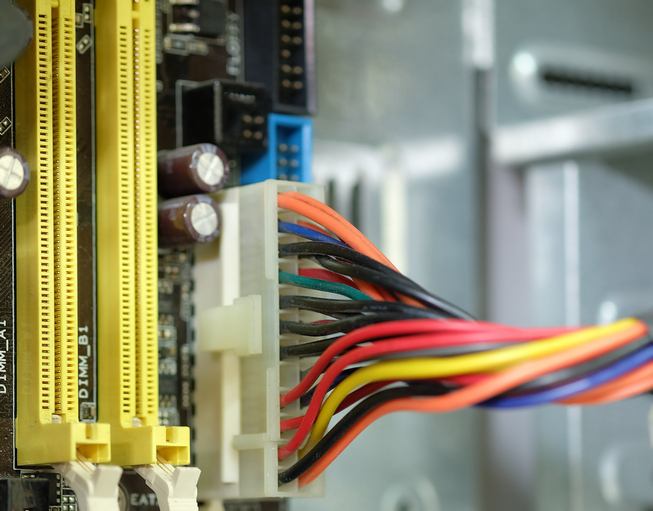
Thermal Management in Wiring Harnesses: Preventing Overheating from the Ground Up
As electronic systems evolve—becoming smaller, faster, and more power-dense—thermal management in wiring harnesses has become a mission-critical concern. For sectors like automotive, industrial automation, consumer electronics, and medical devices, poor thermal control can lead to catastrophic failures, from malfunctioning ECUs to burnt insulation in life-saving equipment.
At Celestix Industries, our deep engineering discipline, stringent quality controls, and certified processes ensure that our wiring harnesses are designed not just to conduct—but to endure. We deliver thermal harness solutions across multiple industries, backed by our commitment to harness thermal design, heat management harness technologies, and in-house harness heat control capabilities.
Why Thermal Management Matters
Wiring harnesses are the vascular system of any electronic or electromechanical assembly. With the growing push toward electrification, high-density PCB integration, and high-current applications like EVs and smart appliances, temperature rise is no longer a marginal issue.
Wiring harness overheating can result in:
Insulation breakdown – leading to shorts, arc faults, or fires
Connector degradation – causing intermittent failures or signal loss
Current derating – reducing system efficiency and performance headroom
Voltage drop – directly impacting powertrain or control system functionality
Premature harness failure – increasing maintenance, warranty costs, and safety risks
For mission-critical applications, even a 5°C thermal delta can shorten lifespan by 20–30%. That makes proactive thermal design, such as wiring harness heat control, essential.
Key Drivers of Heat Build-Up
Heat in wiring harnesses arises from:
I²R losses – electrical resistance of the conductor under load
Ambient environmental factors – enclosures, engine bays, and tight cabinet spaces
Proximity to heat sources – radiators, motors, transformers
High current concentration in small-gauge wires or tight bundles
Substandard materials – low-conductivity metals or inadequate insulation
Understanding these factors informs our heat-resistant harness design, thermal dissipation wiring harness development, and optimized routing strategies.
Celestix’s Approach to Thermal Control in Harness Design
1. Conductor Optimization for Current Load
Our engineers begin by calculating current profiles and derating factors based on the environment. We use:
High-purity copper (99.99%) for superior conductivity
Tinned or silver-plated copper for corrosion resistance
Stranding classes (Class B, Class K) optimized for flexibility and conductor thermal management
We design in accordance with IEC thermal harness standards, factoring in amperage, bundle size, and duty cycle.
2. Thermally Resilient Insulation & Sheathing
Material science plays a critical role. Depending on the application, we use:
PVC: versatile and cost-effective, up to 70°C
XLPE: excellent thermal and chemical resistance, up to 125°C
Silicone: highly flexible and heat-stable to 250°C
PTFE and FEP: chemically inert and operable beyond 250°C
Thermal sleeving harness options: glass-fiber braided sleeving for abrasion and thermal endurance
Our selection is always RoHS harness heat management compliant and meets UL-approved thermal harness requirements.
3. Thermal-Aware Routing and Bundle Management
Using tools like EPLAN, RapidHarness, and CAD modeling, we simulate cable paths to avoid thermal pinch points:
Avoid bundling high-current and signal wires together
Ensure spacing from engines/exhausts >10 cm
Use modular layouts to improve airflow
Ventilated harness solutions for confined spaces
Compact heat-resistant harness routing in dense assemblies
These layouts support flexible heat management harness needs across sectors.
4. Over-Molded Connectors with Heat-Resistant Resins
In our in-house molding unit, we engineer connectors with:
TPU, PBT, and PA66 housings
Flame-retardant resins (UL 94V-0)
Over-molded gaskets for IP67/IP69K sealing
Heat-shrink or back-shell boots for thermal isolation
These features support rugged thermal harness applications in automotive harness heat control, industrial thermal wiring harness, and appliance harness overheating scenarios.
5. Automated Crimping & Crimp Profile Testing
Poor crimps lead to hotspots. At Celestix:
We use automated press tools with in-line crimp force monitoring
Crimp cross-section analysis is performed after every tool change
Pull tests (per ISO 19642) ensure mechanical integrity
Our harnesses meet IPC/WHMA-A-620 Class 3 standards, and every reliable thermal harness is traceable.
6. Simulation-Backed Prototyping and Heat Testing
Our rapid prototyping team conducts:
Thermal mapping with IR thermography
Heat soak testing to simulate worst-case ambient loads
High-current operational trials under controlled conditions
Each simulation validates EV thermal harness management, HV harness thermal management, and aerospace thermal harness design performance.
Real-World Case: Fast-Charging EV System
A prominent EV OEM was experiencing wiring harness overheating in its battery-to-inverter cable assemblies during high-speed charging. The existing harness lacked effective thermal harness solutions.
Celestix Solution:
Redesigned the harness using over-molded silicone-insulated wires
Integrated multi-layer EMI shielding and custom thermal harness solutions
Used silver-plated terminals to reduce contact resistance
Reconfigured the layout based on harness thermal design principles
Results:
Reduced charge time by 18%
Eliminated overheating
Delivered a scalable heat management harness platform
Our Certifications: More Than Just Paper
Thermal reliability isn’t just engineered—it’s audited. Celestix is a reliable thermal harness supplier with certifications in:
ISO 9001:2015, IATF 16949:2016, UL, CE, RoHS, REACH, BIS
IPC/WHMA-A-620, IEC 60228, ISO 6722
Our in-house lab tests every OEM thermal harness solution using:
Pull testing
Thermal cycling
Vibration and humidity endurance
These steps ensure trusted harness thermal solutions from start to finish.
The Celestix Commitment to Thermal Excellence
Effective thermal management in wiring harnesses isn’t just a design requirement—it’s a strategic advantage. At Celestix, our commitment to precision engineering, certified quality systems, and real-world application expertise ensures that every harness we manufacture is thermally resilient and performance-ready.
Whether you're designing for a high-current EV platform, developing an industrial automation control cabinet, or building space-constrained home appliances, our expertise in thermal harness solutions supports your goals from prototype to production.
We don’t just prevent harness overheating—we design each product with heat-resistant harness materials, simulate for thermal dissipation, and validate performance through in-house harness heat control protocols.
Let Celestix be your trusted partner for scalable heat management harness designs. With deep engineering experience and a legacy of reliability, we deliver where others compromise.
Build better. Build cooler. Build with Celestix.