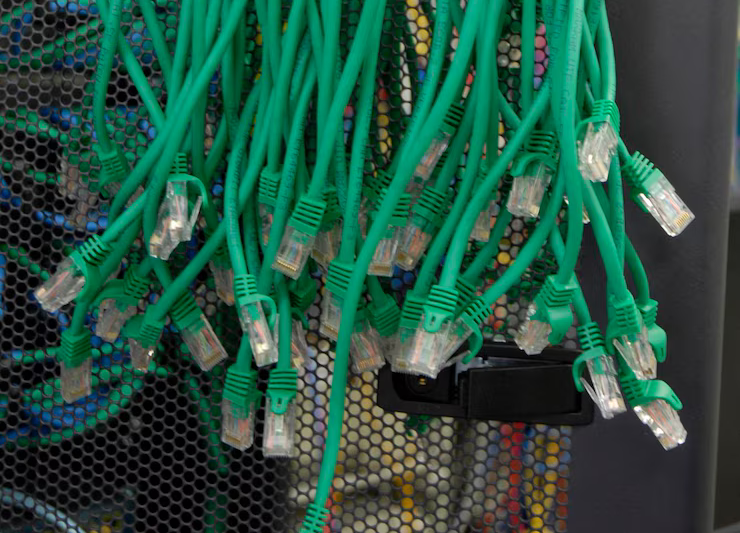
Wiring Harness Design for High-Voltage Applications: Key Considerations
As electric mobility, renewable energy, and high-performance industrial systems continue to evolve, the role of high-voltage wiring harnesses has become more critical than ever. These systems are no longer simple connections—they are engineered lifelines that ensure safety, system performance, and regulatory compliance. Designing a wiring harness high voltage solution involves far more than scaling up a standard design; it requires technical mastery in materials science, environmental adaptability, and high-voltage electrical behavior to deliver reliable HV harness design.
At Celestix Industries India Pvt. Ltd., we specialize in custom high-voltage harness engineering. Whether you're developing an EV high-voltage harness, integrating HV wire harness solutions into industrial systems, or deploying aerospace HV wiring harnesses, we offer end-to-end capabilities to meet the most stringent technical, operational, and compliance requirements. This guide details the key engineering and design principles, along with critical high-voltage harness considerations, needed for building robust, scalable, and application-ready HV solutions.
1. Conductor Selection and Sizing
The conductor is the core of every harness—it determines current-carrying capability, heat generation, and mechanical behavior. Improper conductor selection can lead to voltage drops, inefficiencies, or catastrophic failure.
Material Selection:
Copper: Ideal for high-conductivity and rugged high-voltage harness applications
Aluminum-Copper Hybrids: Lightweight, cost-efficient for aerospace HV wiring harness and EVs
Silver-Plated Copper: Optimal for EMI-sensitive or mission-critical systems
Design Considerations:
Sizing to meet continuous and peak current demands
Maintaining voltage drop below 5% as a voltage drop harness design threshold
Integration with thermal management HV harness systems for heat dissipation
Stranding Classes:
Class B: Suited for fixed installations
Class K: Best for flexible high-voltage wiring in dynamic environments like robotics or electric drivetrains
2. Insulation and Sheathing Materials
Reliable insulation prevents arcing and maintains operational safety under extreme temperatures, vibration, and chemical exposure.
High-Performance Insulation Types:
XLPE: Robust and heat-resistant HV harness insulation for automotive environments
PTFE: Chemical resistance and temperature resilience for rugged high-voltage harness systems
Silicone: Preferred for flexible high-voltage wiring in tight or high-movement zones
Protective Outer Layers:
LSZH: Low toxicity in fire conditions—essential for safety HV harness design
Braided Sleeving / Corrugated PP: Additional mechanical durability
Over-molding & Heat Shrink: Creates compact HV harness solutions with moisture sealing and strain relief
3. Connector and Terminal Engineering
Precision in connectors ensures electrical continuity and mechanical stability in HV harness design.
Engineering Choices:
Use IP67/IP69K-rated connectors for harsh environmental exposure
Implement silver or nickel plating for high-conductivity, corrosion resistance
Employ over-molded connections to reduce EMI ingress and provide shock resistance
Quality Assurance:
Conduct crimp cross-section analysis
Follow ISO 19642 guidelines for pull force testing
Ensure tight dimensional tolerances for trusted HV harness design repeatability
4. Shielding and EMI Protection
High-voltage systems inherently generate electromagnetic fields that can disrupt adjacent electronics. Proper shielding is a non-negotiable requirement.
Shielding Approaches:
Braided Copper Shields: Durable and flexible
Foil + Drain Wire: Ideal for signal lines in mixed-power assemblies
Conductive Over-molded Jackets: Add secondary EMI barriers in compact HV harness solutions
Grounding Best Practices:
Provide continuous coverage with minimal breaks
Separate HV and low-voltage lines in routing
Use star-grounding or bonded ground structures depending on application
5. Thermal and Mechanical Durability
Mechanical stress and heat buildup are leading causes of high-voltage harness degradation.
Key Design Techniques:
Simulate thermal cycling between -40°C to +150°C to mimic field conditions
Perform vibration analysis under ISO and EN standards
Add support using boots, grommets, clips, and secure brackets
Material Compliance:
Ensure all polymers meet UL 94V-0 standards
Follow IEC HV harness standards for material and installation safety
6. Routing and Layout Optimization
Efficient routing boosts performance and minimizes risk.
Best Routing Practices:
Avoid tight bends; maintain a bend radius ≥ 3x outer cable diameter
Prevent contact with moving components or heat zones
Group cables based on function while adhering to separation guidelines
Validation Tools:
Employ digital twin harness simulations for spatial layout
Integrate with 3D CAD assemblies for form-fit-function analysis
7. Standards, Compliance, and Testing
Meeting international safety and quality standards is essential for product approval and user trust.
Mandatory Certifications:
ISO 6722, ISO 19642, IEC 60228 (Automotive and HV wires)
IATF 16949 for automotive suppliers
IPC/WHMA-A-620 Class 3 for aerospace and mission-critical equipment
UL, CE, RoHS high-voltage wiring, REACH, ISO 14001 for global market readiness
Test Protocols:
Hi-Pot Testing: Verifies dielectric strength
IR Testing: Ensures insulation resistance exceeds 100 MΩ
Leakage Current Testing: Monitors current loss across HV paths
8. Simulation and Prototyping
Advanced tools help design right the first time, reducing iterations and field failures.
Simulation Stack:
CAD Harness Simulation for electrical path analysis
3D Modeling to optimize enclosure routing
FEA for mechanical load stress
Thermal and EMI Simulation Harness for real-use scenarios
Celestix Capabilities:
In-house testing lab for high-voltage prototypes
1–2 week prototyping turnaround
Full support for OEM HV harness considerations
Applications of High-Voltage Harnesses
EV & Hybrid Vehicles: HV battery harness design, HV inverter harness design, HV motor harness solutions
Industrial Equipment: High-power automation, robotic arms, heavy drive systems
Renewable Energy: Renewable energy HV harness for inverters, turbines, and storage systems
Aerospace & Defense: EMI-shielded, weight-optimized aerospace HV wiring harness solutions
Medical Systems: Safe, shielded cables for MRI, CT, and other imaging systems
Why Choose Celestix?
Vertically Integrated Manufacturing: From CAD to cable crimp
Accredited Facility: ISO 9001, ISO 14001, IATF 16949, IPC-A-620
Test-Backed Engineering: Pull force, insulation resistance, EMI mitigation
Simulation-Based Design: Trusted by leading OEMs for Celestix HV harness design
Scalable Production: From prototypes to mass-volume scalable HV harness solutions
Let’s Power the Future, Safely
High-voltage wiring harnesses are essential to the future of transportation, energy, and advanced manufacturing. With our commitment to trusted HV harness design, simulation-driven processes, and certified production, Celestix delivers harness systems that perform under pressure and scale with confidence.
Get in touch via our Contact Form to begin your next high-voltage harness application with Celestix.